HOW MICROWAVE ASSISTED COMMINUTION CAN REDUCE
ENERGY USAGE
Comminution (sometimes called particle-size reduction) accounts for up to 70% of the total energy used in mining operations. It involves reducing the size of the ore into smaller particles with the goal of liberating as much valuable mineral as possible. Traditional techniques, like grinding or crushing, are energy intensive with low energy efficiencies (about 91% of the energy is lost). Adding a pre-treatment step, like microwave heating, to soften the ore could increase efficiency and reduce cost. This process is commonly referred to as microwave assisted comminution.
BASICS OF MICROWAVE ASSISTED COMMINUTION
Fundamentally, microwave assisted comminution uses thermal stress to soften the ore. It starts with a generator converting electric energy into microwave energy, and directing it into a chamber via waveguides. Inside the chamber, the microwave energy selectively targets dielectric materials within the ore. Examples of dielectric materials are valuable minerals (like sulphides and some metal oxides), while gangue minerals (worthless minerals like silica) are usually transparent to microwaves and do not heat.
Once exposed to the microwave energy, dipoles in the dielectric material create friction by rotating with the alternating field. This friction creates differential heating and thermal expansion within the ore, resulting in micro-fractures along the grain boundaries, weakening the mineral lattice (often referred to as softening the ore). Softening the ore can make it easier to crush and grind, increase mineral liberation, and reduce the energy required for comminution.
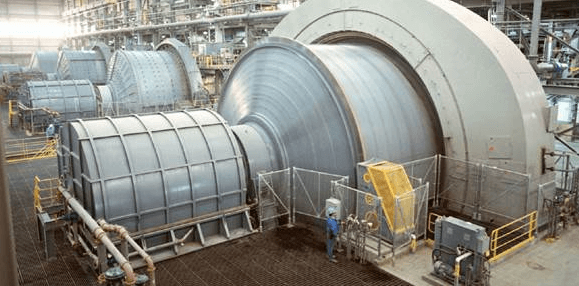
Photo of traditional particle-size reduction equipment at mine sites.
BENEFITS OF PRE-TREATING ORE WITH MICROWAVE
REDUCED ENERGY CONSUMPTION
Microwave pre-treating ore, even for just a few seconds, could significantly reduce energy consumption during particle size reduction, one of the most energy-intensive steps in the mining process. The microwave treatment softens the ore, making it easier to break down during grinding (also known as reducing ore competency). As a result, often less mechanical force is needed to reduce the particle size, leading to lower energy usage. For example, microwave pre-treatment could reduce comminution energy consumption by up to 50%.
INCREASED MINERAL LIBERATION
In addition to reducing energy use, microwave assisted comminution can enhance mineral liberation. The micro-fractures created along mineral boundaries can help separate valuable minerals from gangue minerals more easily. This can result in higher recovery rates of valuable minerals during downstream processes (like flotation and leaching).
CONCLUSION:
REDUCE COMMINUTION ENERGY USAGE WITH MICROWAVE HEATING
Microwave heating could be used as a pre-treatment to reduce energy usage during particle size reduction. Using thermal stress, microwave processing creates fracturing along the mineral boundaries to “soften” the ore. Softening the ore means less energy is required to crush or grind it, and the ore can be more easily broken into smaller size pieces. As a result, microwave assisted comminution of ore could result in energy savings as well as increased mineral liberation.
It’s worth noting the efficiency of adding microwave pre-treatment to comminution can depend on a variety of microwave processing parameters, ore variables (like dielectric and magnetic properties), and throughput requirements (like load mass, size, and position).
Contact NuWave Research to discuss how microwave pre-treatment of ore could optimize your comminution operations.