ELECTROMAGNETIC DRYING: RADIO FREQUENCY AND MICROWAVE
THE DIFFERENCE WAVELENGTHS CAN MAKE
Radio frequency (RF) and microwave drying are both techniques that use electromagnetic energy to dry, but with differing wavelengths and frequencies. RF energy has longer wavelengths (millimeter to kilometer range), but lower frequencies (~13 to 27 MHz) compared to microwaves. Microwave energy has wavelengths between the millimeter to meter range and frequencies between 950 to 2450MHZ. Ultimately, the differing wavelengths and frequencies affect their ideal applications, drying techniques, and processing operations much like between IR and Microwave. Read our blog about the differences between IR and microwave drying to learn more.
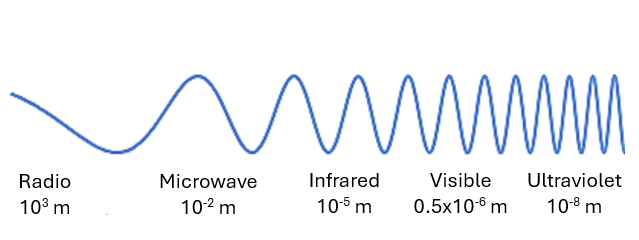
Diagram illustrating radio frequency and microwave wavelengths in the electromagnetic spectrum.
DRYING TECHNIQUES
Radio frequency and microwave drying are efficient drying techniques. This is because they selectively target polar molecules and directly transfer energy (RF or microwave waves) to the molecules without significantly heating the surrounding air. In addition, both rapidly heat the entire material uniformly (a process referred to as volumetric heating), unlike traditional drying methods that heat from surface to core.
In RF systems, a generator converts electricity into radio frequency energy, creating an alternating electric field between two parallel plates called electrodes. The material is then transported between the electrodes. The polar molecules in the material absorb the radio frequency waves and rapidly rotate to align with the changing polarity. This rapid molecular movement causes friction, generating heat throughout the material and causing water to evaporate quickly.
In microwave systems, a generator converts electricity into microwave energy. The microwave energy is then directed towards the material in the chamber via waveguides. The polar molecules in the material absorb the microwaves and rapidly rotate to align to their electric field, causing friction between molecules. This friction converts microwave energy into thermal energy, increasing the temperature throughout the material evaporating water.
TIME
Radio frequency and microwave drying are fast processes compared to traditional methods. This is because of their volumetric processing and selective heating of polar molecules. However, microwave drying is generally faster. Its higher frequencies allow microwave energy to be more readily absorbed by polar molecules in the material compared to RF drying. This causes polar molecules to rotate quicker, leading to faster heating and evaporation of water from the material.
MATERIALS AND END PRODUCT
Because of their volumetric processing, both techniques are great at drying delicate materials and preserving original quality and color. For instance, microwave dried carrots resemble fresh with the same bright orange colors and aromas.
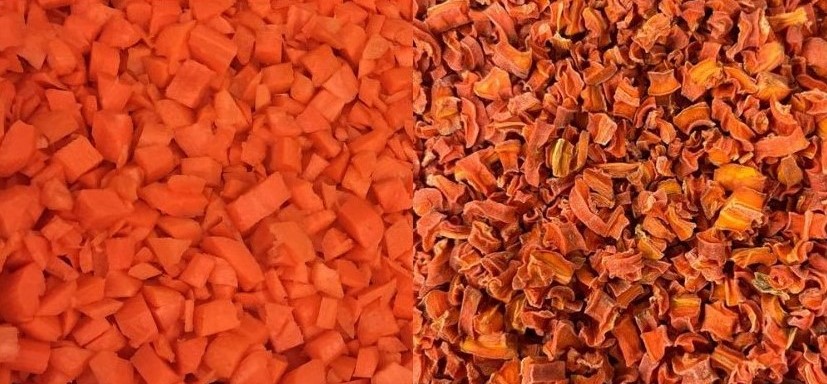
Fresh diced carrots on the left, microwave dried diced carrots on the right.
Although, their applications can differ because their processing occurs at contrasting frequencies and wavelengths. RF drying is ideal for processing uniformly shaped materials (like textiles, grains, crackers, and biscuits) and thicker materials (like wood products). This is because it’s usually able to evenly penetrate material thicker than a few inches and evenly shaped. RF drying irregularly shaped material can result in uneven drying. This is because the RF energy is attracted to different parts of the material depending on its proximity to the electrodes and any material differences in dielectric properties. Alternatively, microwave drying is great for rapidly processing materials of all sorts of shapes and sizes. For example, granular to panel shaped plastic materials, and sliced, diced, or shredded fruits and vegetables.
OPERATIONS
Radio frequency and microwave drying systems can be used as a single step or added to traditional methods for pre- or post-processing. For instance, RF can be used as a post-baking step for cookies, crackers, and biscuits to increase oven band speeds. In addition, RF and microwave systems have greater energy flexibility during operations as they can adjust their energy by zone to accommodate processing speed and in-coming material temperature.
Both radio frequency and microwave drying systems are fully electric and emissions-free drying techniques. As a result, they usually require little to no permits and professional installation services. In addition, their electric drying can offer potential energy savings and reduced fossil fuel emissions by replacing or combining them with traditional gas systems.
With regards to systems, RF systems often have larger footprints because the technology requires large electrodes. RF is limited to a conveyor-based system, but material handling for microwave can vary based on the application. For instance, a conveyor-based microwave system can be used for flat materials like panels and slabs, while paddle- or drum-based microwave system can be used for materials that can be mixed like powder and granular materials. Microwave and RF systems can be built for ambient and vacuum environments. Although, most RF systems are built with ambient environments with the exception of timber and wood RF processing systems. Microwave systems can be built to process in inert atmosphere environments as well, depending on the material and application.
CONCLUSION
Both techniques offer volumetric and electric processing, but microwave drying is generally a faster process for a wider range of applications. Ultimately, the choice between drying techniques will depend upon the material, end-product goal, and business needs. In some cases, a combination of various drying methods might provide the best outcome. Contact us to learn more about microwave drying and what type of materials can benefit from it.